The Hanova manufacturing process
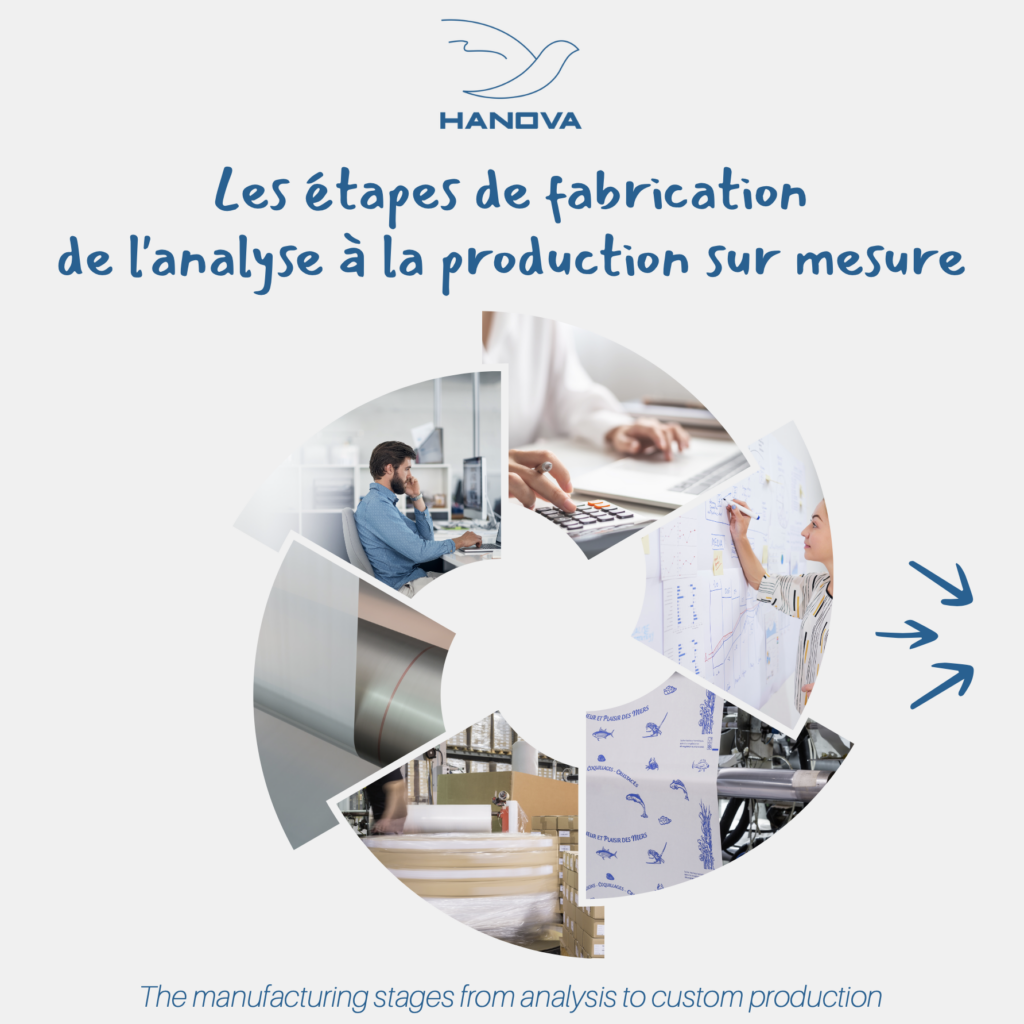
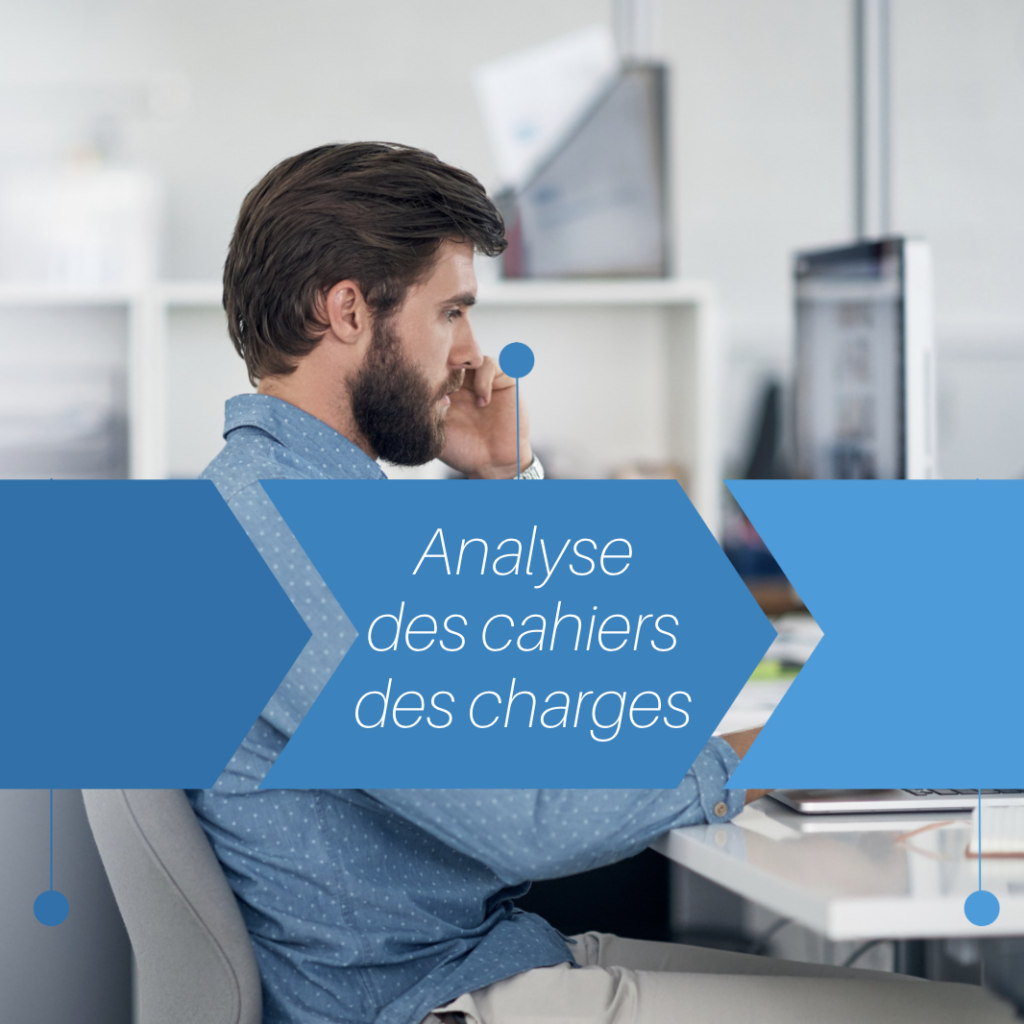
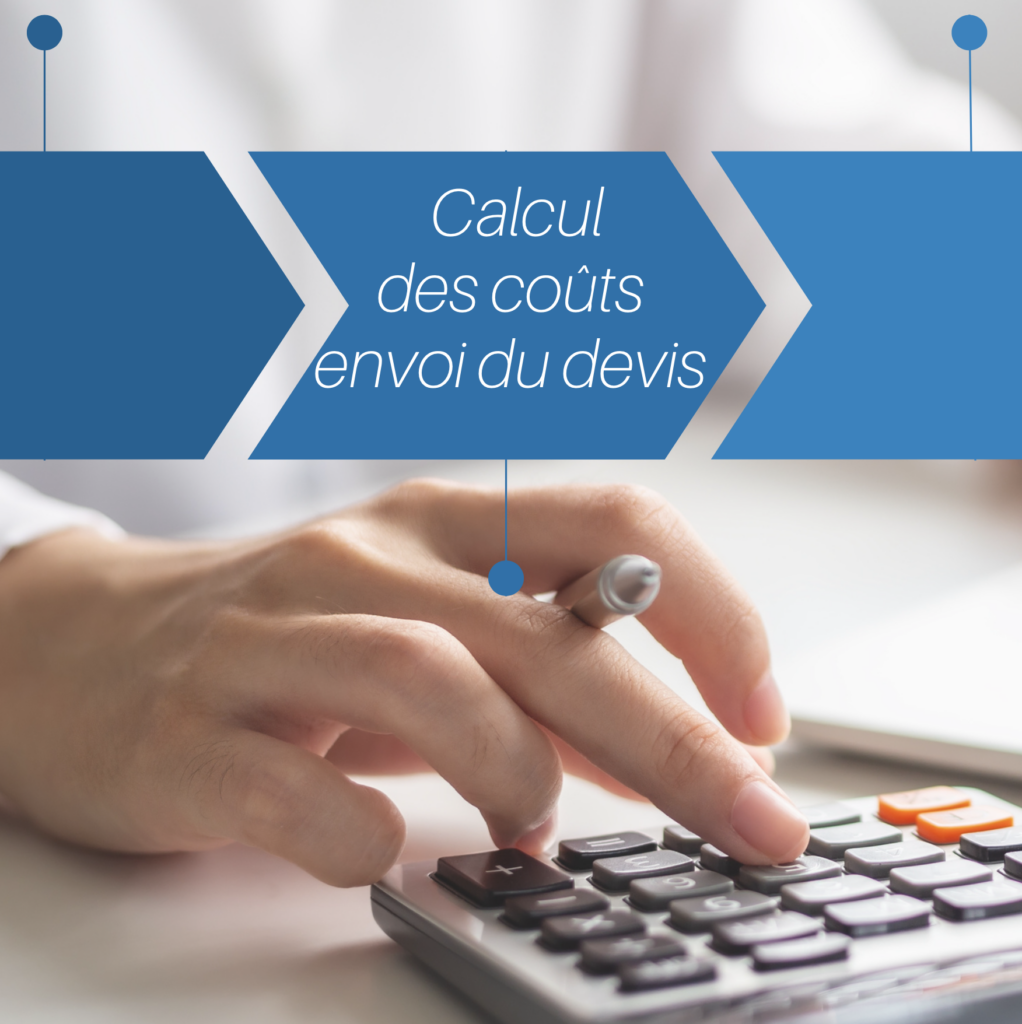
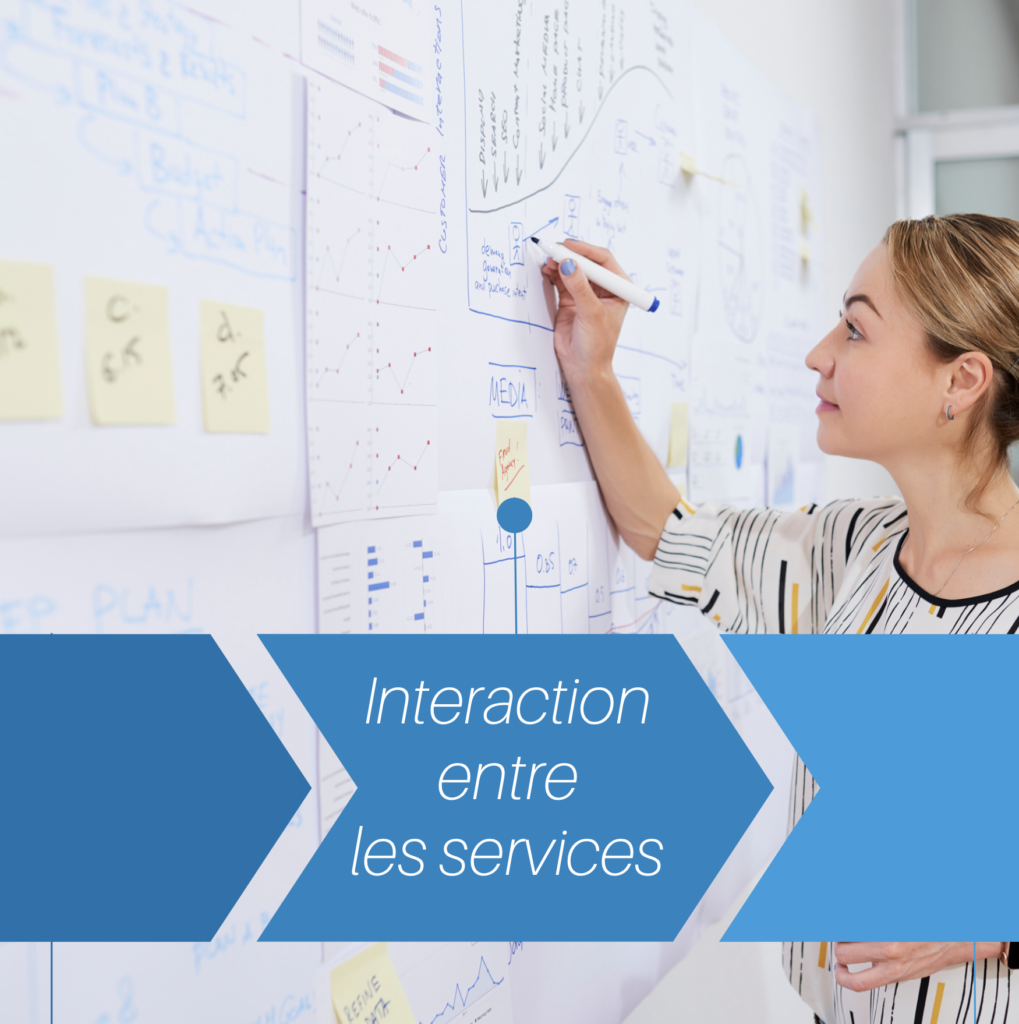
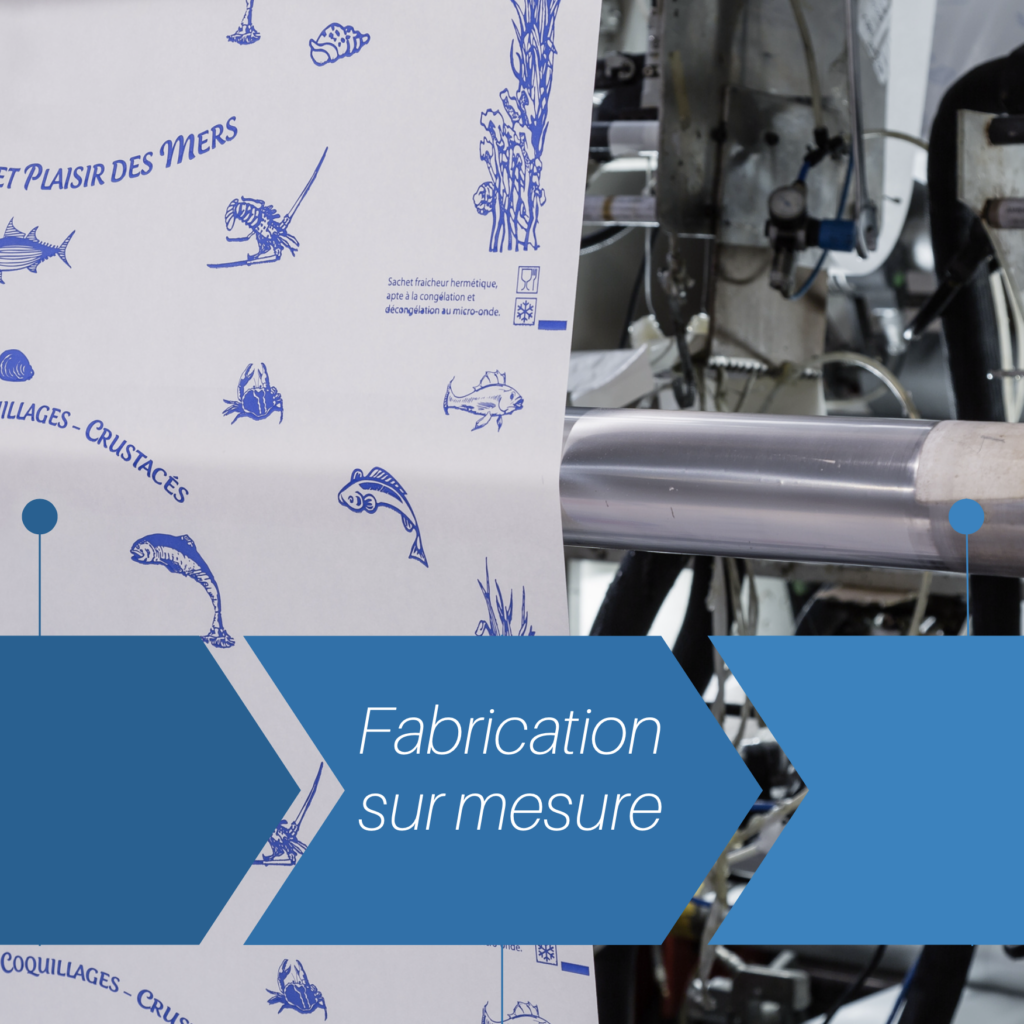
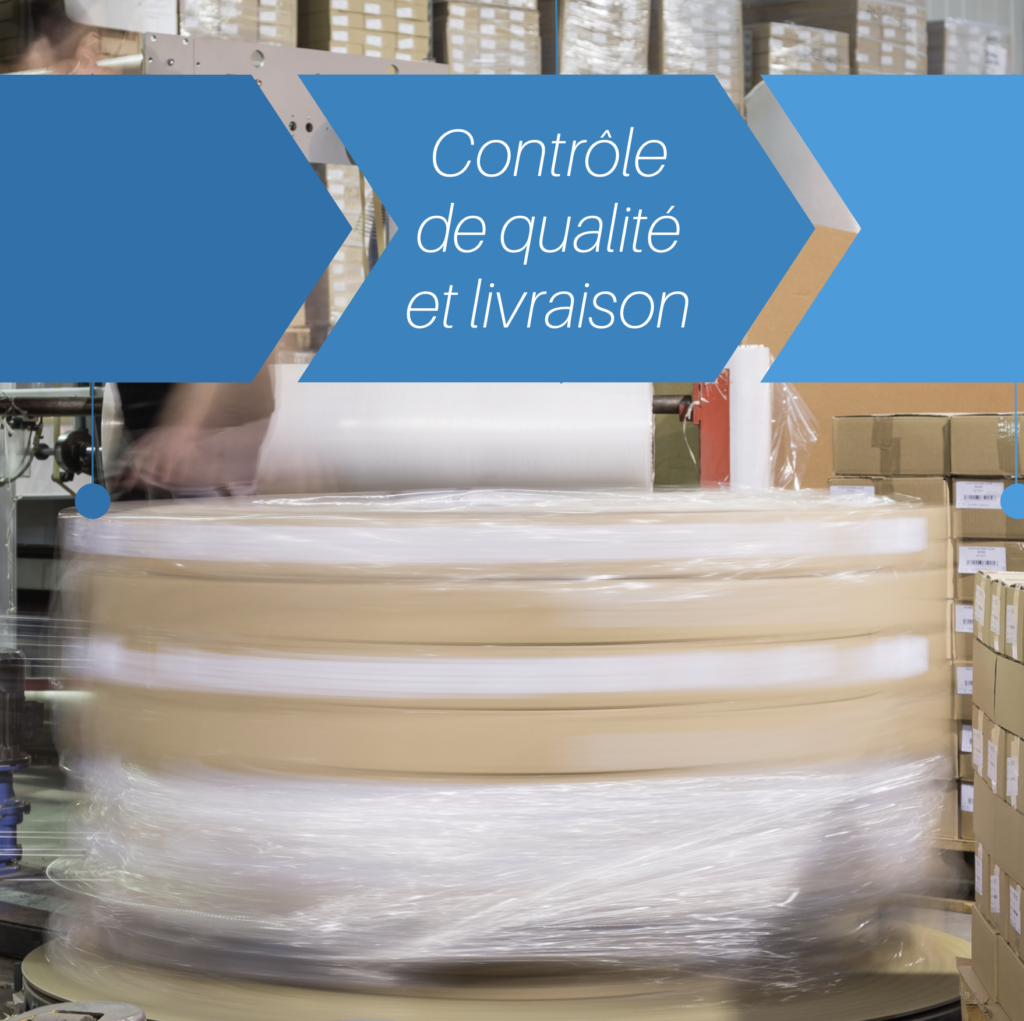
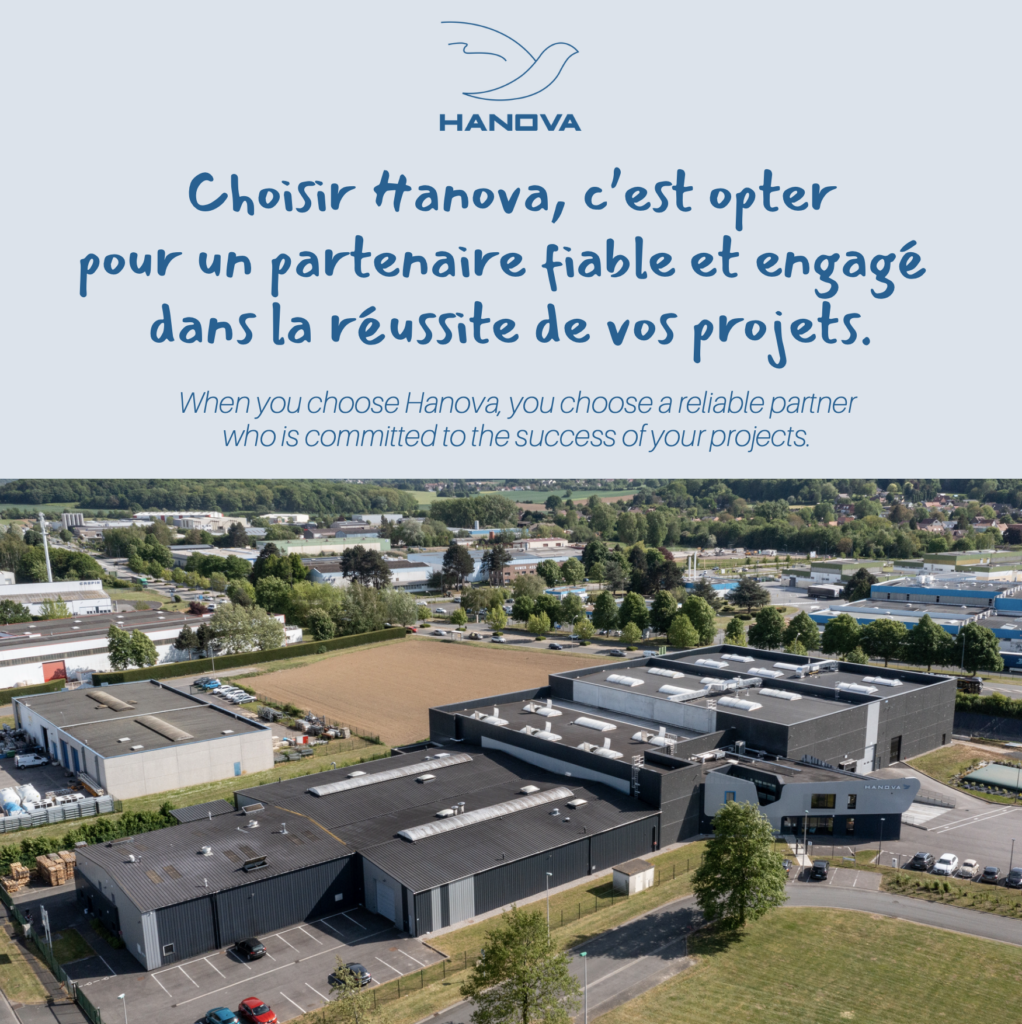
Find out how each stage of our manufacturing process is meticulously planned to ensure high-quality products that meet the specific needs of our customers.
1. Analysis of specifications It all starts with an in-depth analysis of the specifications provided by our customers. Our engineering and design experts work closely with them to define and understand all the specifications. We listen to every need!
2. Our sales team then draws up a detailed quotation, including estimated costs, production and delivery times. We provide transparent and competitive quotes so that every customer has a clear understanding of the costs associated with their project. We can also provide samples.
3. Interaction with the sales and planning departments Once the quotation has been approved, our sales department registers the order and finalises the details of the project with the customer, confirming the final specifications and preparing the necessary contractual documents. Our planning department then confirms the order with the customer, specifying the delivery date. Our administrative team keeps track of all the formalities to ensure a smooth transition to production.
5. Made-to-measure production Mass production then begins in our workshops in Ruitz. Using our expertise and state-of-the-art equipment, we produce bespoke packaging solutions, manufactured with precision and care.
6. Quality control and delivery Before dispatch, our products undergo rigorous quality control to ensure they meet the highest standards. Finally, our logistics team organises delivery so that orders arrive on time and in perfect condition.
Every step, from analysing specifications to custom manufacturing, is designed to ensure maximum customer satisfaction. By combining expertise, advanced technology and responsive customer service, we deliver packaging solutions of the highest quality.
If you had any doubts… Choosing Hanova means choosing a reliable partner committed to the success of your projects.